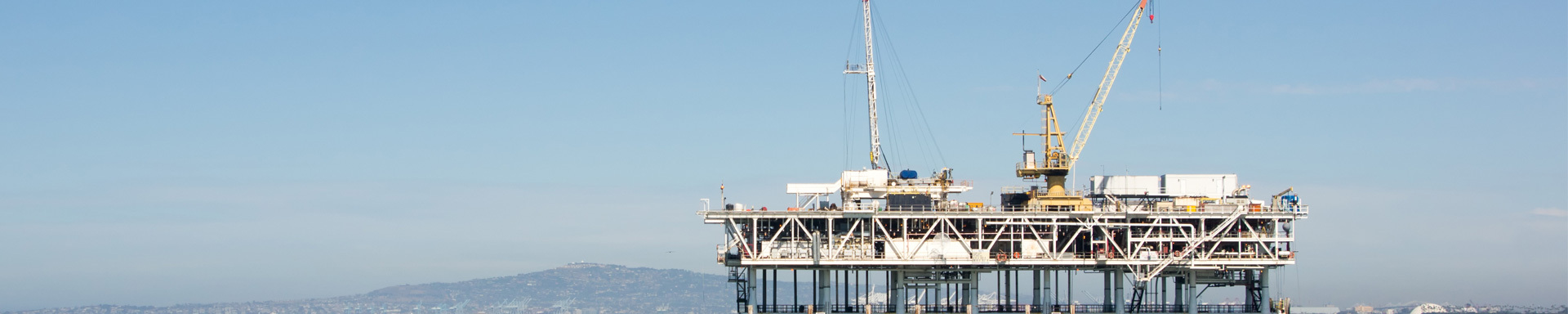
How to Intensively Improve The Service Life Of Oil Drill Pipes
2024-08-08 10:00How to Intensively Improve The Service Life Of Oil Drill Pipes
In recent years, horizontal wells, deep wells and ultra-deep wells, large displacement wells and special wells have increased year by year, and the traditional drill pipes can no longer fully meet the use requirements. The demand for high-strength, high-toughness, intelligent, digital, corrosion-resistant, high-temperature, high-torque and high-sensitivity drill pipes is growing.
Therefore, the research and development and promotion of new drill pipes are more in line with the future development trend of the industry.
Double-shoulder high-torsion drill pipe. This drill pipe has two main advantages:
First, the torsional strength is 30% to 50% higher Drill Pipethan that of the API standard joint;
Second, the water hole is enlarged, and the water hole of the 5"S135 drill pipe joint can be increased from 2-3/4" to 3-1/4". Therefore, this drilling tool meets the needs of large-displacement torque drilling operations and is suitable for drilling deep wells, ultra-deep wells, high-angle wells and horizontal wells.
Smart drill pipe: First developed by Grant Company in the United States, a chip is implanted in the drill pipe joint. During the drilling process, downhole information is transmitted in real time, and the instruments on the ground are analyzed synchronously, which can Improve efficiency.
Aluminum alloy drill pipe: The main advantage is light weight. Under the same strength, the weight is only half of that of steel drill pipe, so it has advantages in equipment, power, transportation, etc., and the wall thickness of the drill pipe is increased, which enhances wear resistance and has a service life of almost twice that of ordinary thin-walled steel drill pipe.
Composite drill pipe: After the composite drill pipe is wound on the reel with carbon fiber, it is covered and sealed by an epoxy composite material. It has high strength-to-weight ratio, ultra-high corrosion resistance and fatigue resistance. The disadvantage is that the wall thickness is large and the current production cost is relatively high.
The alternating stress and torque borne by the lowest part of the whole set of drilling tools in use are the largest. The drilling tools at the "dogleg" in special wells are also very easy to be damaged, which will cause different degrees of loss of the same batch of drilling tools. Referring to the barrel theory, the stability of the whole set of drilling tools is not determined by the strongest, but by the weakest one. Therefore, in actual work, it is necessary to use the same batch of drill pipes reasonably according to the difficulty of drilling and the frequency of use, so as to extend the service life of the drilling tools. During the drilling process, you should always pay attention to the condition of the drilling rig and drill pipe. Once the drill is stuck, hold it. If there are phenomena such as death, the drilling should be stopped immediately or the drilling should be slowed down after re-drilling to prevent the drill pipe from bending and deforming. After completing the operation, the sludge on the drill pipe should be cleaned in time, especially in acid-alkali areas, and anti-corrosion work should be paid attention to. If there are serious problems, the drill pipe should be returned to the factory for repair or scrapped in time. In addition, the drill pipe maintenance cycle should be formulated, and the drill pipe should be regularly treated with rust and dust prevention to extend the service life of the drill pipe.