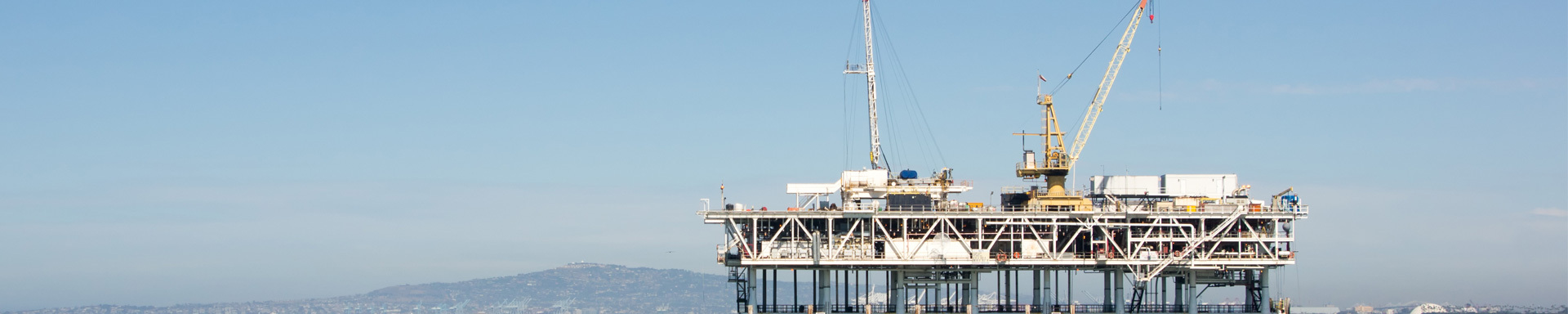
Reasons For Failure Of Drill Pipe Body Found During Drill Pipe Repair
2024-08-31 10:00Reasons For Failure Of Drill Pipe Body Found During Drill Pipe Repair
The reason for failure of the middle part of the drill pipeDrill Pipe body is that the drill pipe has pits due to long-term storage in corrosive media, and there are microcracks around the pits. During the drilling process, the initial cracks are generated at the stress concentration point at the bottom of the pit due to bending alternating stress. As the service process progresses, the microcracks will slowly expand. Due to normal wear and eccentric wear of this part, the wall thickness becomes thinner, which accelerates the crack expansion and quickly reaches the pipe body piercing or even breaking, causing failure accidents.
1) Most of the failure accidents of drill pipe repair pipe body occur at the disappearance of the inner thickening transition zone, accounting for 70%. The reason for failure is that the structure is unreasonable, causing stress concentration and corrosion fatigue. Failure accidents in the middle part of the drill pipe body account for 30%. The failure reason is the result of the combined effect of thinning of the wall thickness caused by abrasive wear and corrosion caused by pits.
2) It is recommended to strengthen the inspection of the pipe body before welding, conduct non-destructive testing of the pipe body for all drill pipes to be welded, and scrap those with serious internal corrosion to ensure the quality of the pipe body; conduct ultrasonic testing around the thickened transition area of the drill pipe to check whether there are defects in the transition area; before welding the drill pipe, the length of the internal thickened transition area and the arc radius where the transition area disappears should be checked. Welding is not allowed for those with an internal thickened transition area <100mm and R <300mm.
3) Strengthen the management of drilling fluid. If conditions permit, the pH value of the drilling fluid should be maintained at 10 or above. When the pump pressure drops, if it can be accurately judged that drilling should be stopped in time, it can prevent major failure accidents caused by drill pipe breakage. Improve the level of drilling technology and reduce the severity of /dogleg0. Low-strength drill pipes are preferred.
Drilling tools refer to tools used in connection with drilling holes and drilling. Equipment, instruments and machinery equipped for special purposes. Such as deep well drilling tools, oil drilling tools, etc. Drilling towers and machine rooms and other complete sets of equipment necessary for drilling and future oil extraction. The drilling tool consists of an active drill pipe, a drill rod, a core tube, a reamer and a drill bit at the bottom. If necessary, a sedimentation tube or a drill collar is added to the top of the core tube. The function of the drilling tool is mainly to transmit the drill pressure and rotation torque to the drill bit during the drilling of rock formations, and to transport drilling flushing fluid to the bottom of the hole to collect rock and mineral cores. All components of the drilling tool are made of high-quality seamless steel pipes with excellent physical and mechanical properties to withstand the alternating load, fatigue and wear of the drilling tool itself during the drilling process.