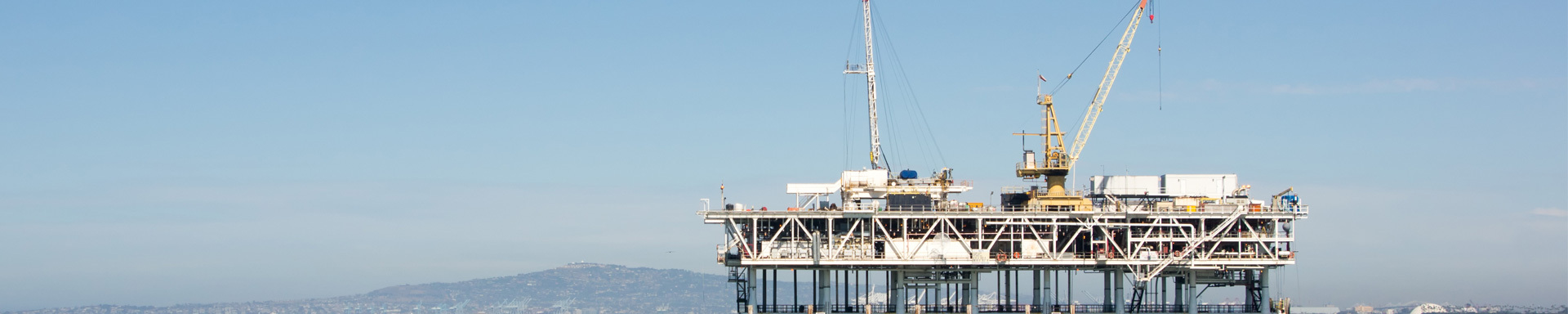
The Requirements For The Use Of Mud Motor
2024-08-18 10:00The Requirements For The Use Of Downhole Drilling Mud Motor
Downhole Drilling Mud MotorDownhole Drilling Mud Motor were originally used to drill vertical holes, mainly for various directional holes and special engineering holes (such as mine freezing holes). The maximum drilling depth is 9023 meters. At present, the smallest diameter of Mud Motor in the world is 44.5 mm and the largest diameter is 304.8 mm. When using Mud Motor for core drilling, a core tube should be added between the drive shaft and the drill bit to take the core.
The Mud Motor consists of a bypass valve, a screw motor (rotor and stator), a universal joint, a bearing and a drive shaft, and its core is the screw motor.
In the mud motor rotor and stator transmission pair, the stator tooth number Z1 is one more than the rotor tooth number Z2: that is, Z1= Z2+1. Their tooth number ratio is usually called the transmission ratio, and it can be selected arbitrarily during design (1:2, 2:3,..., 9:10). A Mud Motor designed for high speed should use a screw motor with a small gear ratio, while a Mud Motor designed for low speed and high torque should use a screw motor with a large gear ratio. As the rotor-stator gear ratio increases, its efficiency gradually tends to decrease; the output torque of the Mud Motor depends on the working pressure drop through the motor, and the output speed depends on the flow rate of the working medium through the screw motor.
During drilling, conventional drilling equipment such as drilling machines, mud pumps, drill rods and drilling towers are still required. When constructing directional drilling, the deflection tool should be oriented with the help of a directional instrument. The deflection tools used in conjunction with the Mud Motor include bent joints, bent outer pipes and eccentric blocks. Using a Mud Motor to construct directional holes can improve the quality of drilling holes, provide accurate geological data, save footage, reduce costs, and solve many engineering problems that cannot be constructed. Therefore, it is a special tool for drilling projects.
The service life of a Mud Motor is generally 150 to 200 hours. Its weak link is that the stator rubber has low high temperature resistance and the bearing is easily damaged. Step up the research and development of wear-resistant and high-temperature resistant elastic materials and reliable bearing systems for manufacturing stators, so as to significantly improve the working life of Mud Motor. And develop low-speed and high-torque screws for deep and ultra-deep holes.
1. Drilling fluid requirements: Mud Motor can work effectively for all kinds of muds, including oil-based muds, emulsified muds, clay muds, and even water. The viscosity and specific gravity of mud have little effect on the drill, but have a direct impact on the pressure of the entire system. If the pressure under the recommended displacement is greater than the rated pump pressure value, the mud displacement must be reduced, or it is necessary to reduce the pressure drop through the drill and the drill bit. Impurities such as sand particles in the mud will affect the performance of the drill and accelerate the wear of the bearings and motor stators. Therefore, the sand content in the mud must be controlled below 1%. Each type of drill has its own input flow range. Only within this range can the drill have a higher efficiency. Generally, the middle value of the input flow range should be taken as the optimal input flow value.
2. Mud pressure requirements: When the drill tool is suspended, the displacement remains unchanged, and the mud pressure drop through the drill tool remains unchanged. As the drill bit contacts the bottom of the well, the drilling pressure increases, the mud circulation pressure increases, and the pump pressure also increases. The driller can use the following formula to control the operation: Drilling pump pressure = circulating pump pressure + drilling tool load pressure drop Circulating pump pressure is the pump pressure when the drill tool does not contact the bottom of the well, also called off-bottom pump pressure. When the drill tool increases the torque, the pump pressure will rise. At this time, the reading of the pressure gauge is called drilling pump pressure. Off-bottom pump pressure is not a constant. It changes with the well depth and mud characteristics. However, in actual operation, it is not necessary to measure the accuracy of the circulating pump pressure at any time. Generally, the off-bottom pump pressure after each single connection is taken as an approximate value. This can fully meet the accuracy requirements of the formula. When the drilling tool is working, when the drilling pump pressure reaches the maximum recommended pressure, the drill tool generates the best torque. Continuing to increase the drilling pressure will increase the pump pressure. When it exceeds the maximum design pressure, the motor may brake. At this time, the drilling pressure should be reduced immediately to prevent internal damage to the drill tool.