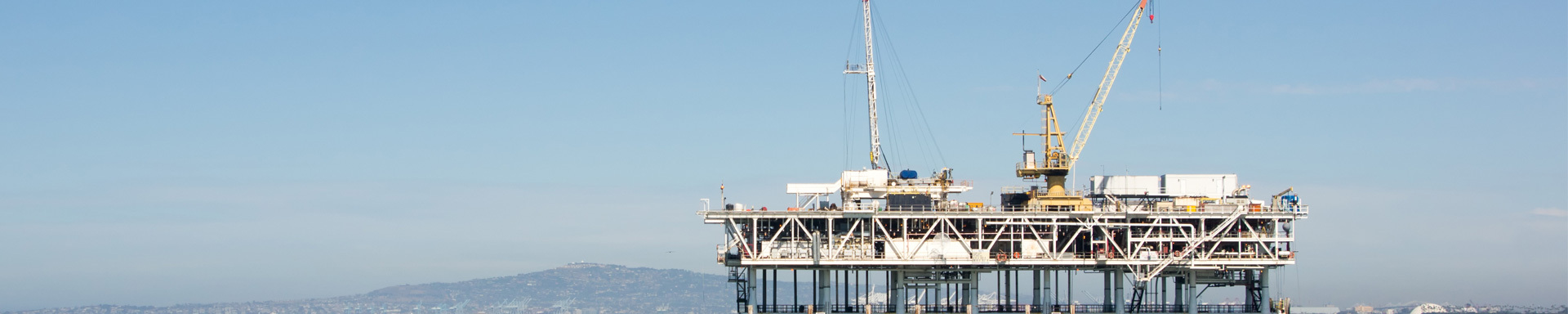
The production process of oil drill pipe is divided into three parts
2024-08-12 10:00Drill PipeThe production process of oil drill pipe is divided into three parts
The production of drill pipe generally includes three parts: pipe end thickening, tool joint processing, friction welding and subsequent processing.
1. Pipe end thickening
The pipe body material of oil drill pipe is low-carbon alloy steel. The round steel billet of continuous casting and rolling is heated in a large rotary furnace and then enters the extension machine and the mandrel automatic piercing machine for forming. After heating again, the inner and outer diameters are refined and straightened to enter the forging process. Since the weld of oil drill pipe is the weakest link in the use process, the seamless pipe must be thickened at both ends of the pipe body before welding to increase the thickness to improve the strength of the weak parts, so that the overall strength of the weld is greater than the overall strength of the pipe body. According to the different pipe diameters, it is generally divided into three types: internal and external thickening, internal thickening, and external thickening, among which the internal and external thickening type is the main one. The process of pipe end thickening is first to heat and equalize the pipe end of the seamless pipe; secondly, the pipe end is pierced by hydraulic or pneumatic means, the outer surface is formed by the mold, and the inner surface is naturally formed by the temperature gradient; finally, the entire pipe body is heat treated, straightened, and non-destructive inspection is performed. The key technology of pipe end thickening is the forming of the inner surface transition zone, because this part is the weakest and most complex in use, and about 70% of accidents occur in this part, so it is very important to the quality of the drill pipe.
2. Tool joint processing
The material of the tool joint is generally medium carbon alloy steel. The blank is stamped three times after heating, and then machined after normalizing. First, the inner hole, outer circle, and end face of the blank are turned, and then the joint is tempered and heat treated to obtain comprehensive mechanical properties. Finally, the joint is threaded, and the threaded part must be copper plated or phosphated to prevent sticking during use.
The quality of the joint depends on the two key processes of heat treatment and thread processing. Heat treatment organization directly affects the mechanical properties of the joint, so advanced drill pipe factories use fully automatic continuous controllable atmosphere protection heating, oil or water-based quenching agent quenching, and reducing atmosphere protection during the joint heating process to ensure that the workpiece is not oxidized, decarburized, and carburized. After quenching and tempering the joint, surface hardness testing and magnetic particle inspection are carried out one by one. After heat treatment, thread processing is carried out. The drill pipe thread is a coarse-pitch tapered thread. In the connection process of the drill pipe, the thread plays a key role. Therefore, thread processing is mostly carried out by high-precision CNC machine tools, and the thread close distance, pitch, taper, tooth height and other parameters of the processed joints are measured one by one to ensure the thread buckle type and precision requirements, thereby effectively ensuring the connection performance of the drill pipe joint.
3. Friction welding and subsequent treatment
Friction welding of drill pipe is an important part of the entire drill pipe production. In order to ensure the welding quality, almost all drill pipe factories use fully automatic friction welding machines and are equipped with welding parameter monitoring devices to automatically monitor and record parameters such as friction time, friction pressure, upsetting pressure, upsetting time and shortening during welding, so as to ensure the quality of the weld. After welding, the welding burrs need to be removed, the welding heat affected zone needs to be tempered, and the weld needs to be inspected by non-destructive testing. Among them, the tempering heat treatment of the weld is very important. Almost all manufacturers use medium frequency heating to carry out the treatment, and automatically record parameters such as heating temperature, heating time, insulation time, and quenching time. The advantages of this weld heat treatment are: the heating heat affected zone is narrow and the heating time is short; the weld zone has uniform and stable structure and reliable performance; the residual stress on the surface of the weld zone is small.