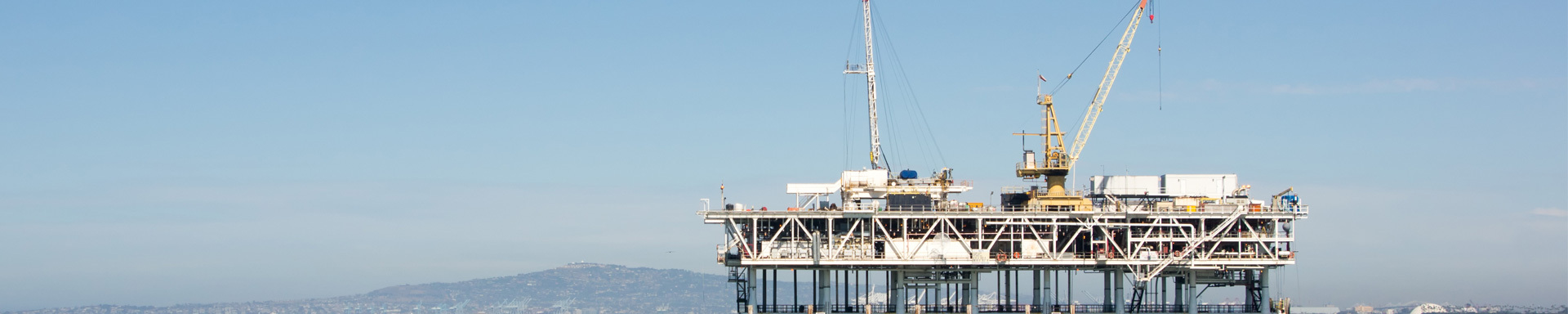
- Home
- >
- Products
- >
- Sucker Rod
- >
Sucker Rod
The sucker rod can be divided into two categories: solid sucker rod and hollow sucker rod.
There are four grades: C,D,K,H, meeting different strength requests.
Sucker rod couplings are essential components in oilfield pumping equipment. A complete sucker rod is typically composed of numerous short sucker rods connected by couplings, with lengths often exceeding several kilometers. It is challenging to ensure concentricity between these short sucker rods, leading to inevitable wear and tear on the couplings during the up and down pumping process.
However, existing coupling technologies face several shortcomings:
1. The coupling body of the sucker rod is generally made of iron, making it susceptible to corrosion during usage. This results in a relatively short lifespan for the couplings, requiring frequent replacements. Not only does this increase the overall cost of couplings, but it also necessitates the tedious reassembly of short coupliSucker Rod Coupling nSucker Rodgs, hindering the improvement of pumping efficiency.
2. Current coupling bodies are typically of a regular circular shape, leading to significant friction between the coupling and the oil pipe during the up and down pumping process. This further reduces the coupling's lifespan.
3. In existing technologies, an outer layer is often added to the coupling's outer wall to enhance corrosion resistance and reduce wear. Materials such as engineering plastics and rubber are commonly chosen for these outer layers. However, a significant issue arises in high-temperature and high-pressure environments down the oil well, as these outer layers tend to detach, losing their protective function."
To address these challenges, innovative approaches can be implemented in sucker rod coupling design. Introducing corrosion-resistant materials for the coupling body, such as stainless steel or alloys, can significantly extend the coupling's lifespan, reducing the need for frequent replacements and minimizing assembly hassles.
Additionally, exploring non-circular shapes for coupling bodies can help reduce friction with the oil pipe, enhancing the overall durability of the coupling during pumping operations. Advanced coatings or surface treatments can further contribute to wear resistance and improve the coupling's performance in harsh downhole conditions.
Furthermore, alternative methods for protective outer layers, such as advanced ceramics or composite materials, could be explored to overcome the issue of detachment in high-temperature and high-pressure environments. These innovations aim to optimize sucker rod coupling reliability, increase operational efficiency, and ultimately reduce maintenance costs in oilfield pumping systems.
Specification:
Sucker Rod Specifications and main dimensions | |||||
Specifications | Connecting rod size (mm) | Nominal diameter of thread(mm) | Outside diameter(mm) | Length | Class |
5/8 T | 16 | 15/16 | 38.1 | 101.6/4 | T |
3/4 T | 19 | 1/16 | 41.3 | ||
7/8 T | 22 | 3/16 | 46 | ||
1 T | 25 | 3/8 | 55.6 |